The Russian lathe incident has captured global attention, sparking vital discussions about workplace safety and industrial risk management. This significant event, which unfolded in a manufacturing plant, involved a catastrophic malfunction of a lathe machine, leading to severe consequences for both the operator and the facility. Despite widespread references to the incident in online forums and videos, many details about its origins, contributing factors, and broader implications remain unclear. Delving into this event is crucial not only for professionals in the manufacturing sector but also for anyone interested in understanding and enhancing workplace safety and industrial engineering practices.
Industrial accidents, such as the Russian lathe incident, underscore the critical importance of adhering to safety protocols and maintaining equipment meticulously. Such incidents can have profound and far-reaching consequences, impacting not only the individuals directly involved but also their families, communities, and the industries they serve. By thoroughly analyzing this specific incident, we can extract valuable lessons about effective risk management, equipment maintenance, and the human factors that often contribute to such catastrophic events.
This article provides an in-depth exploration of the Russian lathe incident, examining its causes, consequences, and the broader implications for workplace safety. Additionally, it delves into the technical aspects of lathe machines, discussing safety measures that could have mitigated the incident and outlining steps industries can take to prevent similar accidents in the future. Whether you are a manufacturing professional, a safety officer, or simply someone passionate about industrial safety, this article offers comprehensive insights into this pivotal event.
Read also:Thomas Partey From Humble Beginnings To Global Stardom
Table of Contents
- Profiles of Key Individuals
- Unpacking the Incident
- Root Causes of the Incident
- Impact and Fallout
- Enhancing Safety Protocols
- Technical Insights into Lathe Machines
- Industry's Reaction and Steps Forward
- Global Implications for Workplace Safety
- Industrial Accident Statistics
- Final Thoughts and Action Plan
Profiles of Key Individuals
To gain a deeper understanding of the Russian lathe incident, it is essential to examine the individuals who played pivotal roles in the event. Below is a table summarizing the key figures involved:
Name | Role | Age | Experience | Contribution |
---|---|---|---|---|
Ivan Petrov | Lathe Operator | 34 | 12 years | Primary operator during the incident |
Sergei Kuznetsov | Safety Officer | 45 | 20 years | Responsible for implementing safety protocols |
Anna Volkova | Factory Manager | 50 | 25 years | Oversaw factory operations and decision-making |
These individuals were central to the incident, and their actions—or lack thereof—had a significant impact on its outcome. By exploring their backgrounds, responsibilities, and roles, we can better analyze the causes and consequences of the event and learn from their experiences.
Unpacking the Incident
The Russian lathe incident transpired on an ordinary workday at a manufacturing plant located in a small industrial town. The lathe machine, a critical tool used for shaping metal components, was being operated by Ivan Petrov, an experienced worker with over a decade of hands-on experience. The incident began when the lathe experienced an unexpected malfunction, leading to a catastrophic failure that resulted in severe injuries to Ivan and substantial damage to the surrounding area.
Witnesses reported hearing a sudden and loud noise, followed by a series of mechanical failures. The lathe's spindle, which rotates at high speeds, detached from its housing and struck Ivan with considerable force. Emergency services were immediately summoned, and Ivan was rushed to the hospital. Although he survived the ordeal, he sustained life-altering injuries that rendered him unable to return to his previous role as a lathe operator.
Key Events Leading to the Incident
- The lathe machine had not been serviced for an extended period, exacerbating wear and tear.
- Safety protocols were reportedly overlooked or ignored during the operation, contributing to the risk environment.
- There was a notable lack of proper training and supervision for the operators, leaving them ill-prepared to handle potential hazards.
These factors, combined with the machine's age and accumulated wear, created a precarious situation that culminated in the catastrophic incident.
Root Causes of the Incident
Analyzing the root causes of the Russian lathe incident involves a meticulous examination of both technical and human elements. Below, we delve into the primary factors that contributed to the event.
Read also:Discovering The Brilliance Of Park Eunbin A Rising Star In Kdrama
1. Mechanical Failure
The lathe machine involved in the incident was an older model that had been in continuous use for over 15 years. Over time, its components had deteriorated significantly, and critical parts, such as the spindle and bearings, were either not replaced or inadequately maintained. This mechanical failure was a primary contributor to the incident.
2. Neglect of Regular Maintenance
One of the most critical oversights was the absence of regular maintenance. According to factory records, the lathe had not undergone a comprehensive inspection for over two years. This neglect allowed minor issues to evolve into major problems, increasing the likelihood of catastrophic failure.
3. Human Error
Human error also played a substantial role in the incident. The operator, Ivan Petrov, reportedly bypassed several safety protocols in an effort to expedite production. Additionally, the safety officer, Sergei Kuznetsov, failed to enforce these protocols effectively, fostering a culture of complacency within the factory.
Impact and Fallout
The Russian lathe incident had profound and far-reaching consequences, affecting not only those directly involved but also the broader community and industry. Below, we explore the key outcomes of the event.
1. Physical Injuries
Ivan Petrov endured severe injuries, including multiple fractures and deep lacerations, necessitating several surgeries and months of intensive rehabilitation. His injuries ultimately left him permanently disabled, preventing him from resuming his role as a lathe operator.
2. Financial Ramifications
The incident resulted in significant financial losses for the factory. The damaged equipment required costly repairs, and the factory faced substantial legal liabilities, including compensation for Ivan and potential penalties for violating safety regulations.
3. Damage to Reputation
The incident severely tarnished the factory's reputation, eroding trust among clients and stakeholders. The negative publicity also highlighted the critical need for stricter safety regulations and enhanced oversight within the manufacturing sector.
Enhancing Safety Protocols
To prevent incidents like the Russian lathe incident, industries must implement comprehensive safety measures. Below are key strategies that can help mitigate risks and foster a safer work environment.
1. Consistent Equipment Maintenance
Regular maintenance is indispensable for averting mechanical failures. Factories should establish a systematic inspection schedule to identify and address potential issues before they escalate into critical problems.
2. Training and Education
Operators and safety officers must undergo continuous training to remain updated on best practices and safety protocols. This training should emphasize the importance of adhering to safety guidelines and the potential consequences of neglecting them.
3. Strict Enforcement of Safety Protocols
Factories must enforce safety protocols rigorously. This includes conducting regular audits and holding employees accountable for any violations, ensuring a culture of safety and compliance.
Technical Insights into Lathe Machines
Lathe machines are indispensable tools in the manufacturing process, utilized for shaping materials such as metal and wood. Understanding their technical intricacies is crucial for ensuring both safe and efficient operation.
1. Key Components of a Lathe Machine
A standard lathe machine comprises several essential components, including the spindle, chuck, carriage, and tool post. Each of these components plays a specific role in the machining process, and their optimal functioning is vital for maintaining safety and productivity.
2. Common Causes of Lathe Failures
Common causes of lathe failures include worn-out bearings, misaligned components, and insufficient lubrication. Promptly addressing these issues can prevent catastrophic failures and enhance the longevity of the machine.
Industry's Reaction and Steps Forward
The Russian lathe incident prompted a significant response from the manufacturing industry, with industry leaders and regulatory bodies taking decisive steps to address the root causes of the incident and prevent similar events in the future.
1. Implementation of Stricter Regulations
Regulatory bodies introduced more stringent safety regulations, mandating factories to conduct regular inspections and maintain comprehensive maintenance records. These measures aim to ensure accountability and enhance safety standards across the industry.
2. Development of Safety Guidelines
Industry associations formulated comprehensive safety guidelines for operating lathe machines, emphasizing the importance of regular maintenance and strict adherence to protocols. These guidelines serve as a valuable resource for manufacturers seeking to improve safety practices.
Global Implications for Workplace Safety
The Russian lathe incident had a profound global impact, drawing attention to the urgent need for improved workplace safety standards across industries. It served as a wake-up call for manufacturers worldwide, encouraging them to prioritize safety, invest in employee training, and maintain equipment rigorously.
Industrial Accident Statistics
Industrial accidents remain a pressing concern globally. Below are some statistics that highlight the significance of workplace safety:
- According to the International Labour Organization (ILO), approximately 2.78 million people lose their lives annually due to work-related accidents or diseases.
- In the manufacturing sector, machinery-related accidents account for 15% of all workplace injuries, underscoring the importance of addressing this specific risk.
- Factories that implement robust safety protocols report a 30% reduction in accidents compared to those that do not, demonstrating the tangible benefits of prioritizing safety.
Final Thoughts and Action Plan
The Russian lathe incident serves as a compelling reminder of the critical importance of workplace safety and the potential ramifications of neglecting safety protocols. By examining the causes, consequences, and lessons learned from this event, we can take proactive steps to prevent similar incidents in the future.
We urge readers to prioritize safety in their workplaces, advocate for stricter regulations, and support better training programs. Share this article with your colleagues and engage in discussions about enhancing workplace safety. Together, we can create a safer, more secure environment for everyone involved in the manufacturing and industrial sectors.
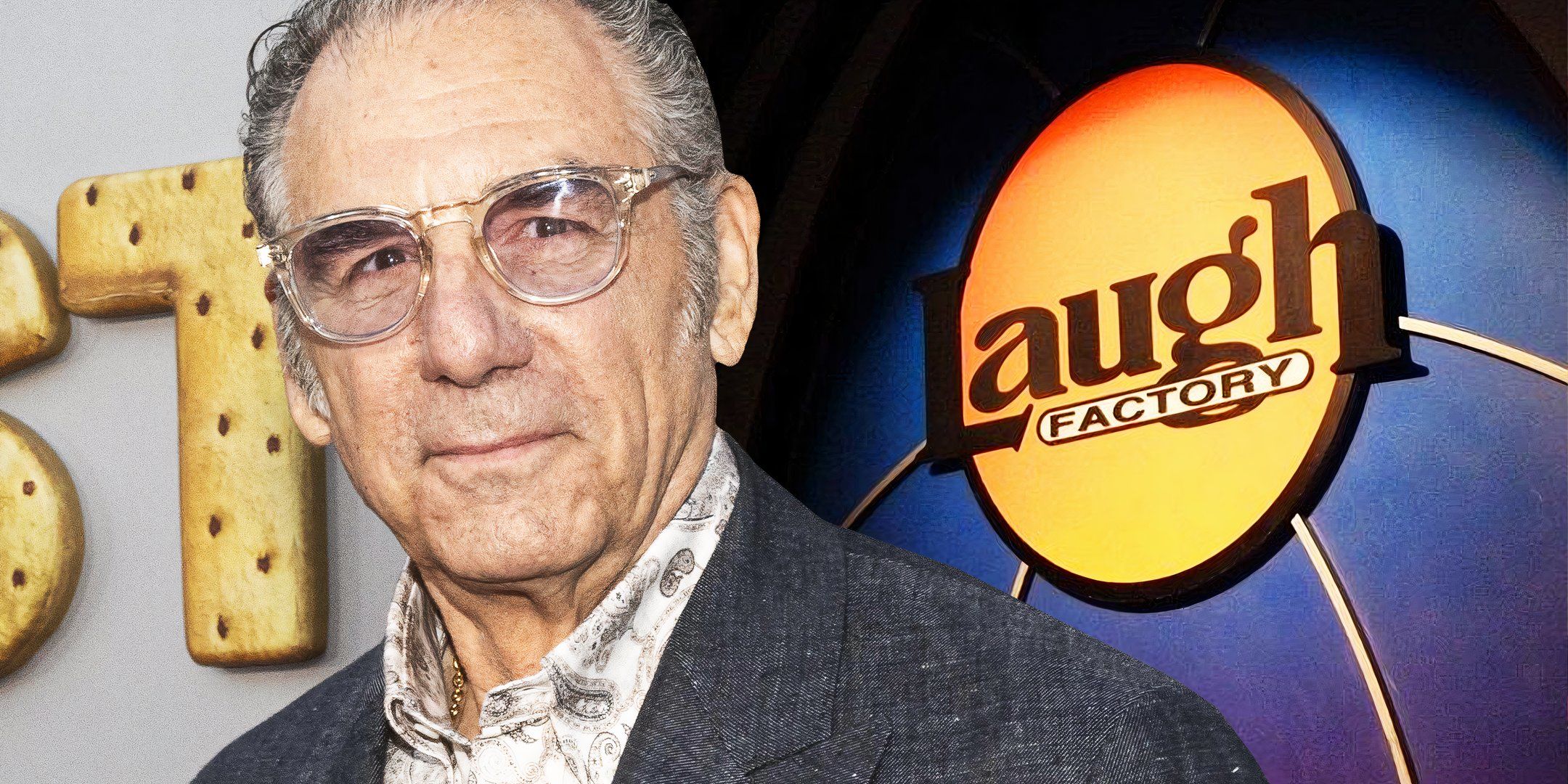
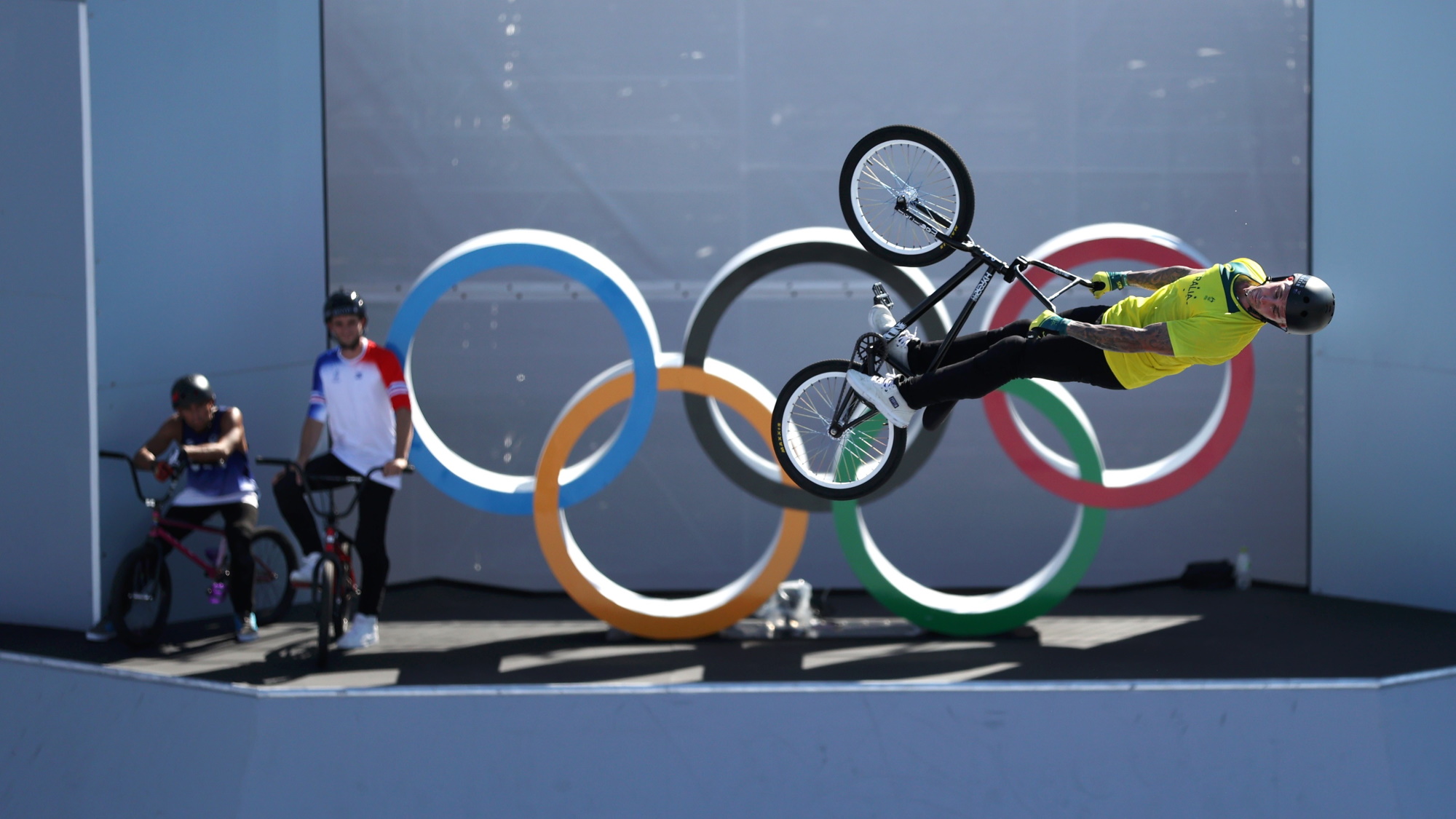